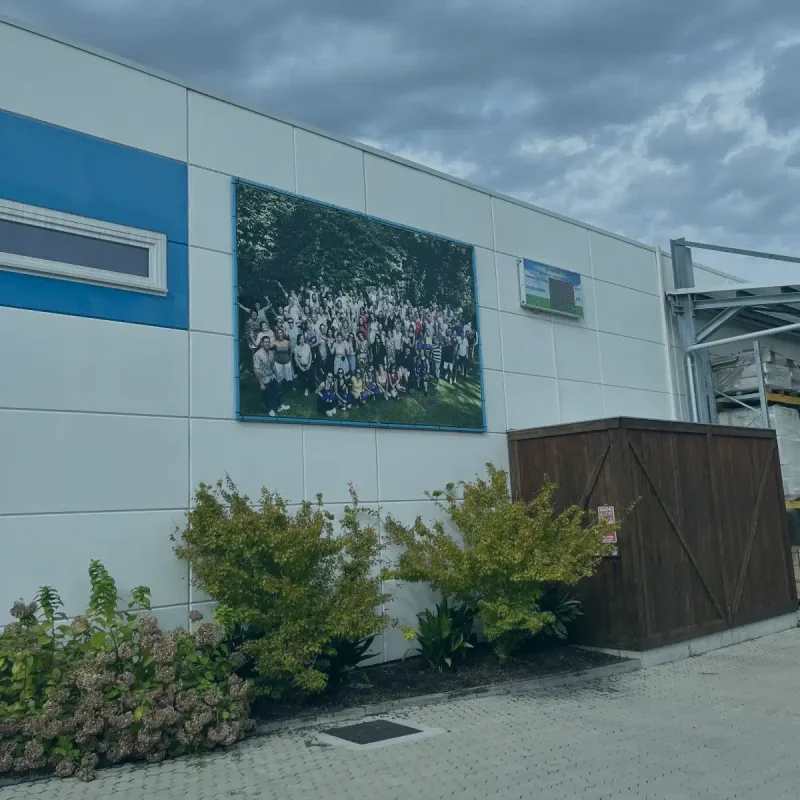
Vector Spa - a Benefit Company
Based in Castellanza (VA), Vector Spa is a leader in international shipping, specializing in air, sea, land, and rail transport.
With a global network covering strategic markets such as China, India, South Korea, Brazil, and the United States, Vector delivers tailored logistics solutions for industries like pharmaceuticals, defense, and hazardous materials. The company stands out for its commitment to innovation and sustainability, recognized by the EcoVadis Gold Meda.
Customer
Goals
Reduce time spent locating and positioning goods
Improve the accuracy of package placement
Enhance the physical and mental well-being of operators
Achieved Results
6% productivity increase
Localization accuracy within 50 cm
Significant reduction in shipping errors
Decrease in operator workload
The challenge
Improving traceability for more efficient cross-docking
Vector turned to KFI to address a key challenge in its warehouse management. Despite high efficiency in pick-up and delivery phases, the company saw room for improvement in the traceability of load units within its warehouse. Once inside, goods would often “disappear from the radar.”
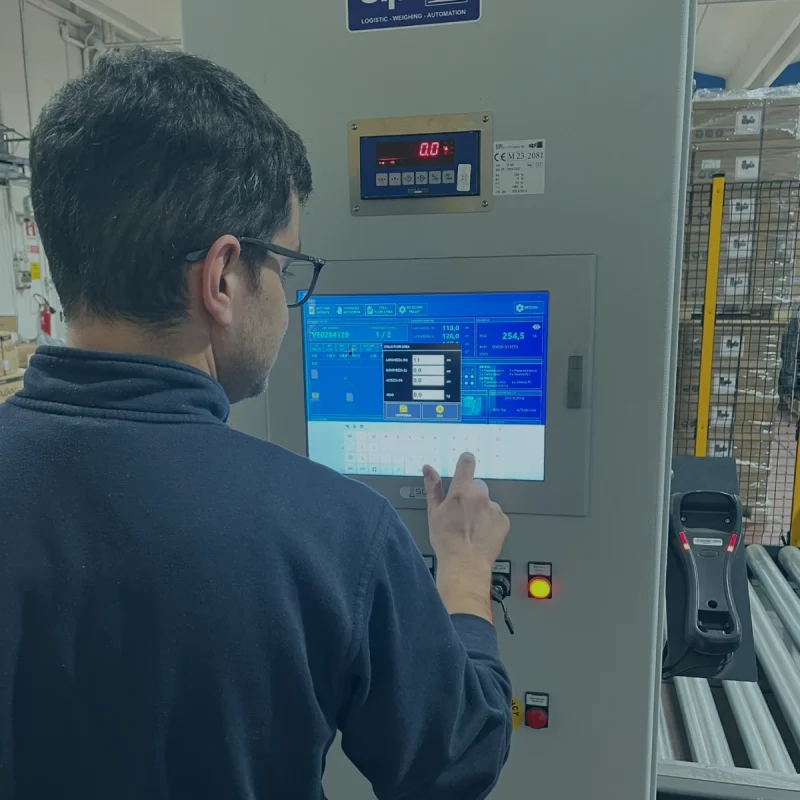
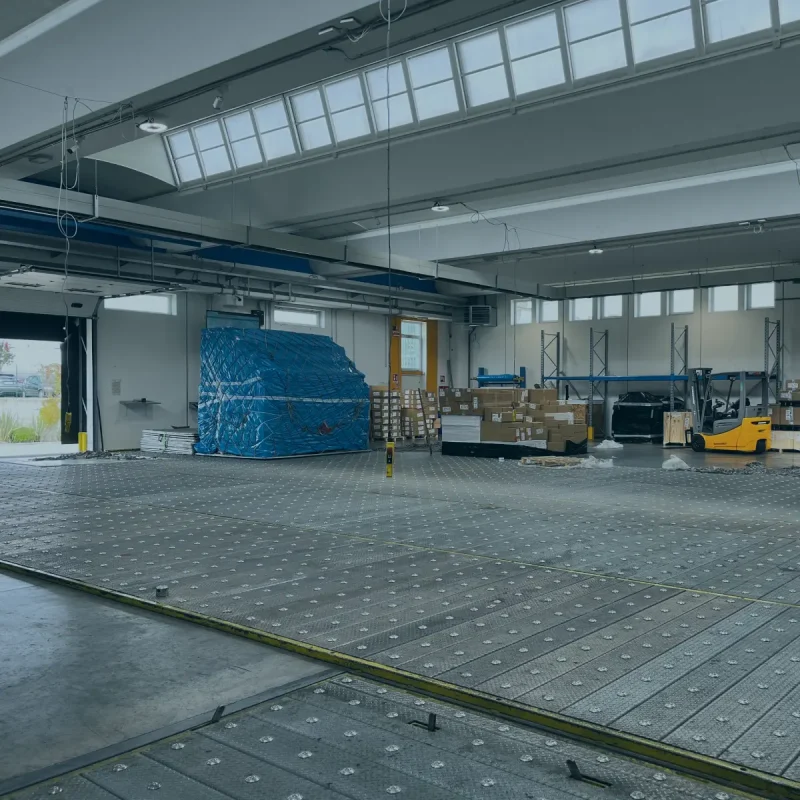
Even though the warehouse was organized into destination-specific zones, the pace of daily operations sometimes led to inconsistent pallet placement.
The lack of a system providing comprehensive visibility of package locations slowed processes, resulting in inefficient searches and shipping delays.
The solution
A WES to redefine transit warehouse managemen
To tackle this challenge, KFI implemented LOJIST, a WES platform that integrates data collected by Zebra mobile computers and RTLS tags into Vector’s information systems. This orchestration of warehouse processes is driven by new, optimized management logic.
On an operational level, goods are initially scanned by a dynamic machine that measures their weight and ensures their security. Operators then use Zebra TC52 devices to scan the barcodes of load units and receive precise instructions on where to place the pallets.
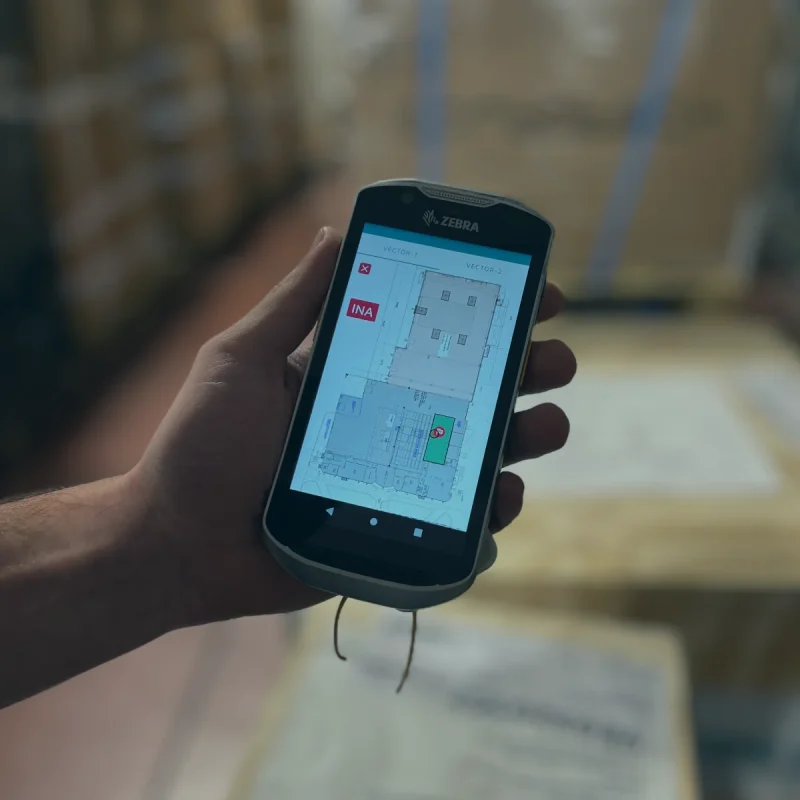
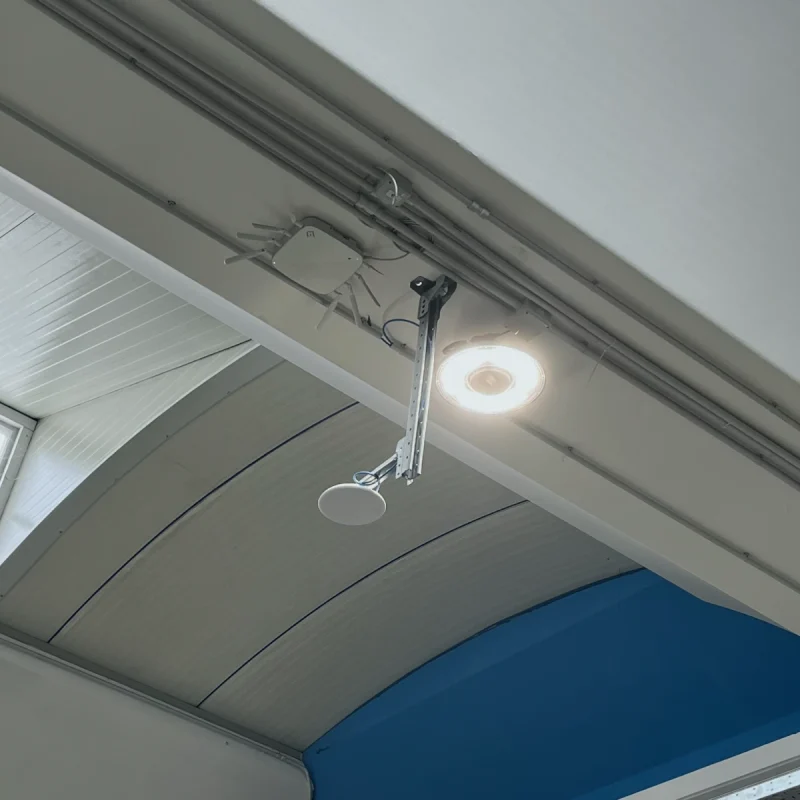
KFI’s WES system, which is also integrated with the compactable warehouse, enables operators to manage aisle openings and closures directly from handheld devices, optimizing the use of the entire space. Finally, thanks to RTLS tags associated with the devices and supported by a dedicated antenna infrastructure, the position of each package is instantly recorded and displayed on an interactive map.
After placement, goods are scanned again to confirm their exact location, updating the system with the coordinates provided by the RTLS tag when the label is read. During the shipping phase, operators can use their mobile computers to consult the warehouse’s digital map and locate packages with accuracy up to 50 cm. This allows for quick retrieval and ensures a smooth and efficient operational flow.
LOJIST
Through its WES platform, KFI excels in integrating RTLS and AIDC technologies into business processes and systems for monitoring products, assets, and people.
Acting as an interface with ERP, WMS, MES, and other management systems, LOJIST provides centralized access to data derived from traceability solutions, facilitating the orchestration of business processes.
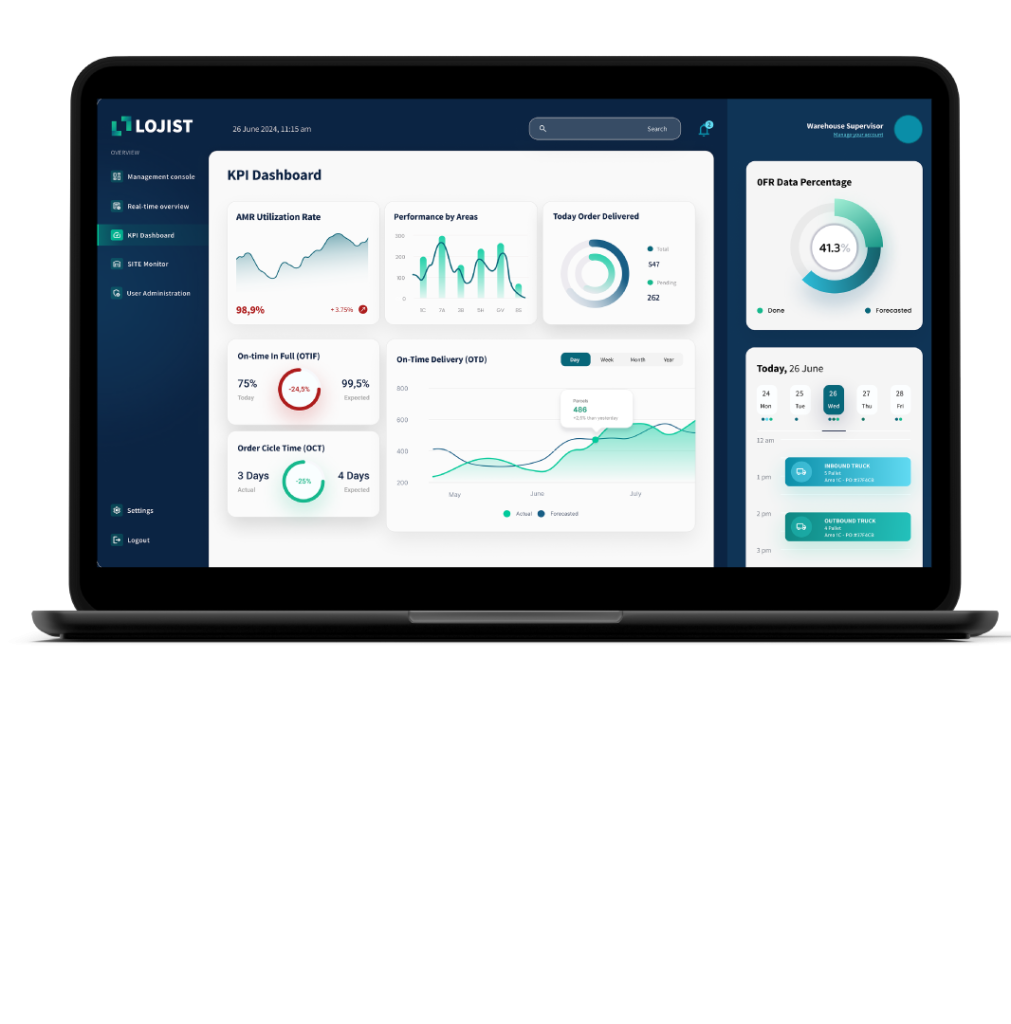
The results
LOJIST: The key to unprecedented productivity and precision
The implementation of the WES system has brought significant improvements for Vector, both in operational capacity and precision.
Overall productivity has seen a noticeable increase, thanks to a drastic reduction in pallet preparation times, which previously could take up to 2 hours.
This acceleration in activities also allows operators to save about 30 minutes per day, helping them avoid extra hours and improving their work-life balance.
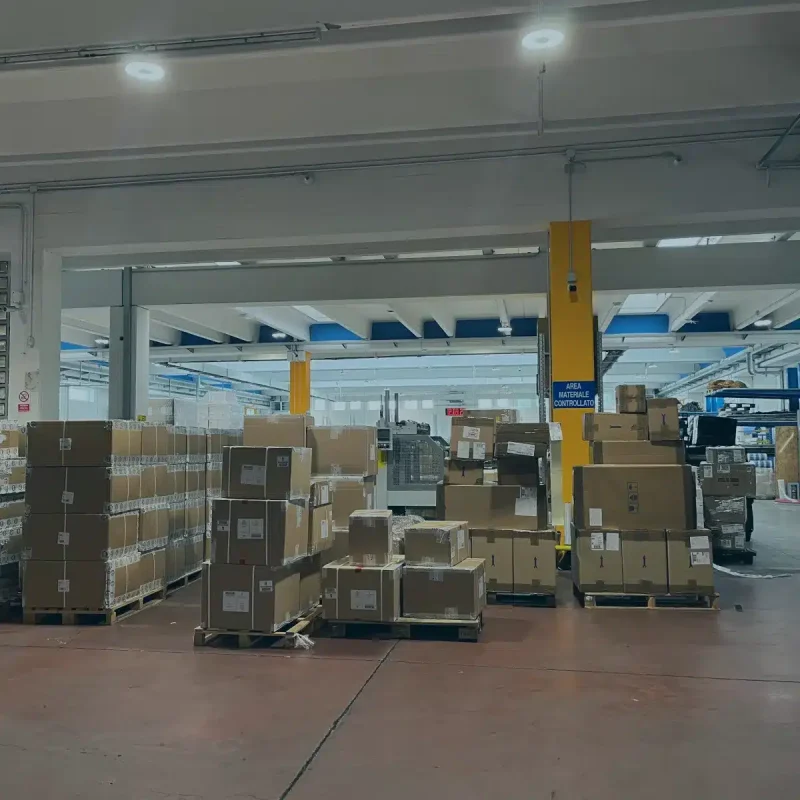
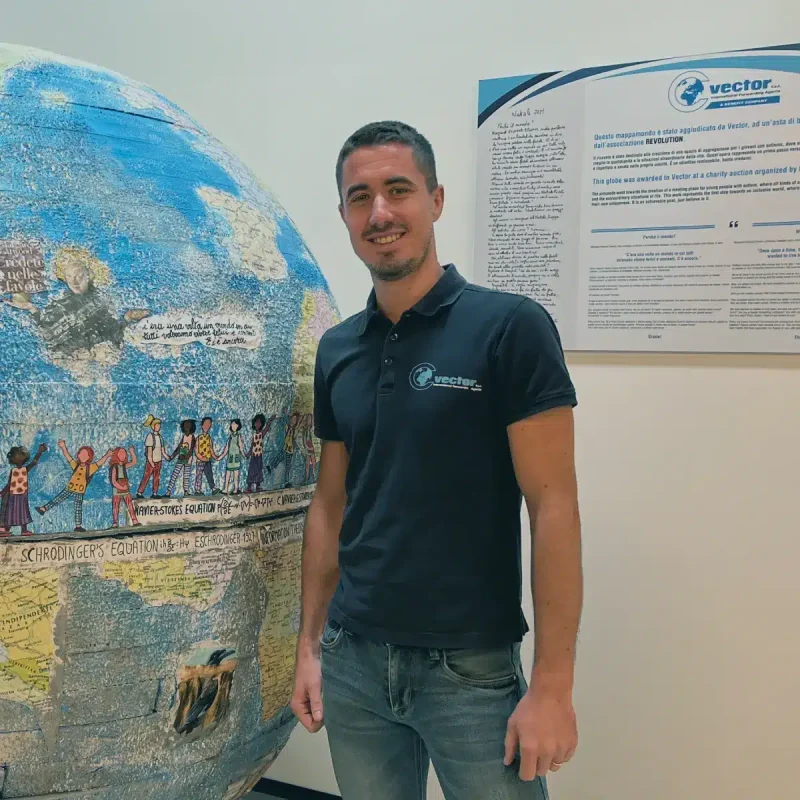
“Initially, the idea of implementing a new system raised concerns, but we were pleasantly surprised to find that its intuitiveness makes it accessible to everyone, from younger employees to more experienced operators. The integration of LOJIST and RTLS technology, along with other implementations and innovations introduced over time, allowed us to nearly double our pallet preparation record from 64 to 116. This reduced work time and boosted productivity by 6%. Not only did it enhance efficiency, but it also led to a reduction in errors and greater precision in operations without compromising service quality”.
Ivan Ravasio, Logistics Manager
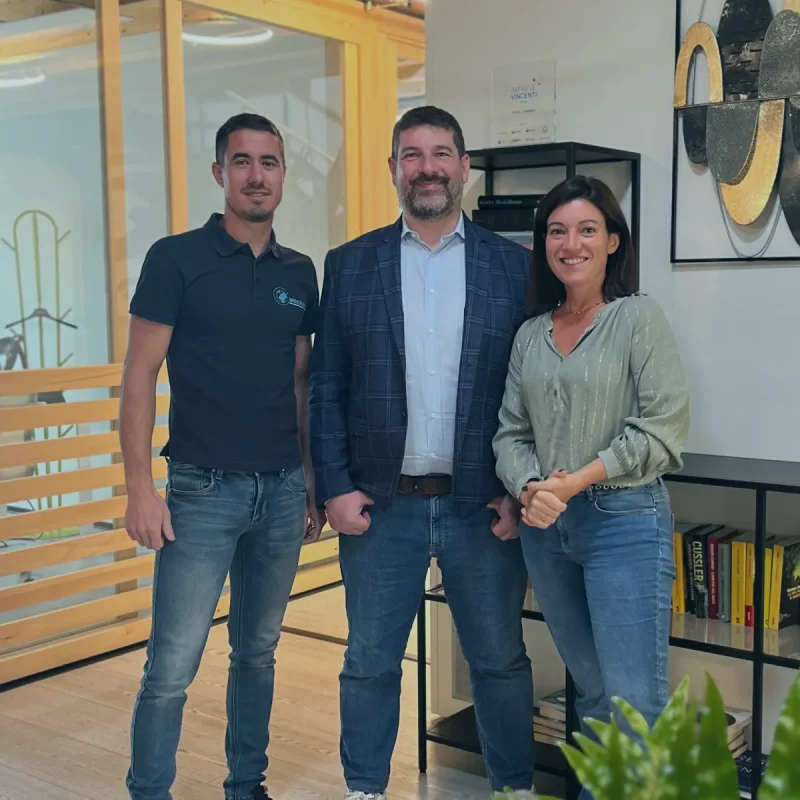
“This success contributes to a broader initiative. As a Benefit Corporation, Vector is committed to making a positive impact on the environment and society, acting as a catalyst for change. The digitalization of the process has led to tangible improvements in our operators’ quality of life, reducing overtime and enhancing their work-life balance. One of our main objectives is indeed the sustainability of work and the well-being of our people, and technology has proven to be a fundamental ally in this mission”.
Camilla Buttà, Sustainability & Communication Manager